How to improve the cleaning effect of the screen changer
The cleaning of the screen changer is divided into 3 steps: TEG cleaning, high pressure water gun cleaning and ultrasonic cleaning.
The extension of TEG cooking time TEG is three glycols, which is a colorless transparent neutral oil liquid. The boiling point is 276 degrees, and it has alcoholysis and dissolution to polyester under heating condition [2]. TEG cleaning is based on TEG solvent, heating cooking, dissolving polyester melt on the screen changer. The melt filter core under the rigid dismantle, wrapped in polyester melt, must be cooked at a TEG steaming tank and removed at a constant temperature of 285 degrees centigrade at 4H. Remove the filter core and find that some melts are still not completely dissolved. Therefore, the constant temperature time is increased from 4H to more than 6h, so that all the melt of the adhesive on the filter core is dissolved. At the same time, two times TEG cooking method is adopted, the dismantled filter core is reloaded into the basket, and the two time cooking is carried out in order to further increase the effect of cooking and cleaning.
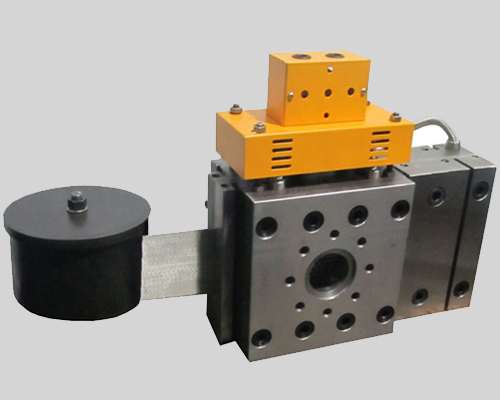
It is necessary to strengthen the high pressure water gun to rinse the TEG filter. Because it is dirty, it must be washed with high pressure water gun. The outer filter is used to replace the net, and impurities remain in the outer layer of the filter screen. For this purpose, a specially designed high pressure water gun is used to flush the impurities out from inside to outside. Meanwhile, the outer protective cover of the filter element is removed to enhance the cleaning effect. In order to clean the filter core to the maximum, 10 roots were taken randomly from a set of filter core, and 5 of them were removed randomly, then the filter core was cleaned with high pressure water gun and 2H was cleaned by ultrasonic wave, and the bubble point test was done, and the comparison result was shown in Table 2. It can be seen that in the stage of high pressure water gun washing and ultrasonic cleaning, the iron cover of the filter core is removed, and it is easier to clean the filter core.
It is necessary to clean the ultrasonic cleaning because of the small molecular impurity at high pressure, easily squeezed into the inner of the filter core, and it is difficult to wash out with high pressure water gun. In order to find out the cleaning time, 1 groups of experiments were carried out. The results are shown in Table 3. Increasing ultrasonic cleaning time alone is not the way. Therefore, the ultrasonic cleaning time is fixed at 2~3h.
After using ultrasonic cleaning, some of the filter impurities are removed, but some of them remain inside the filter screen. In order to remove this part of impurities, after demonstration, a 1.6MPa steam reverse blow production line was built to filter the core blowback to remove the internal impurities to the maximum extent. It has been proved by practice that the effect is remarkable.